AS9100 Calibration Requirements
When I talk about manufacturing and production within the aerospace sector, I emphasize the crucial role of meticulous quality control. Calibration, by definition, checks the precision and accuracy of the measuring equipment, and this is where AS9100 calibration requirements takes center stage. AS9100 is a widely adopted quality management system standard specifically tailored for the aerospace industry. The standard ensures that there’s a high level of trust in the production process, given that even minor errors can have serious implications when it comes to aircraft and space vehicles.
Calibration under AS9100 doesn’t just help in maintaining equipment; it elevates the entire aerospace production landscape to a standard where safety and reliability aren’t just goals but guarantees. Adhering strictly to calibration requirements ensures that manufacturing outputs consistently meet the lofty expectations associated with aerospace products.
That brings us to the calibration requirements within the AS9100 framework. Calibration isn’t just a once-and-done event; it’s an ongoing commitment to precision. In the next section, I’ll unpack the specific clause dedicated to calibration. Knowing what this clause entails is vital, as it lays the groundwork for adherence to the broader standard.
📘 ISO/IEC 17025 Quality Manual Template
Accelerate your lab’s accreditation process with our comprehensive Quality Manual Template, designed to align with ISO/IEC 17025:2017 standards.
- Fully editable and customizable to fit your laboratory’s needs.
- Includes all necessary procedures, forms, and policies.
- Structured to facilitate easy implementation and compliance.
- Developed by experts with extensive ISO/IEC 17025 experience.
What is the Calibration Clause of AS9100
The calibration clause of AS9100 is more than a set of rules; it’s a foundational element ensuring that measurement instruments used in the aerospace industry produce accurate and reliable results. This clause is typically known as 7.1.5 – Monitoring and measuring resources, within the AS9100D standard. It lays out the specifics for controlling, calibrating, and maintaining the tools and equipment that are essential for verification and validation of aerospace products.
When you delve into clause 7.1.5, you find its main goals are to retain measurement traceability and to foster confidence in the measurements. By adhering to the clause’s standards, aerospace manufacturers are able to guarantee that their instruments are properly calibrated to national or international references. Additionally, the clause mandates consistent calibration procedures across the board.
The practical outcome? Each piece of measuring equipment used across the aerospace industry has a known accuracy and is matched to standardized units of measurement. Such rigorous control is crucial, considering even the smallest measurement discrepancy can have major ramifications in this field.
Next up, we’ll explore the basic requirements laid out by the AS9100 standards for calibration. Key points will address not only the type of equipment that needs to be calibrated but also the methods used, and the expertise required to perform these calibrations accurately.
What Are the Basic Requirements of Calibration?
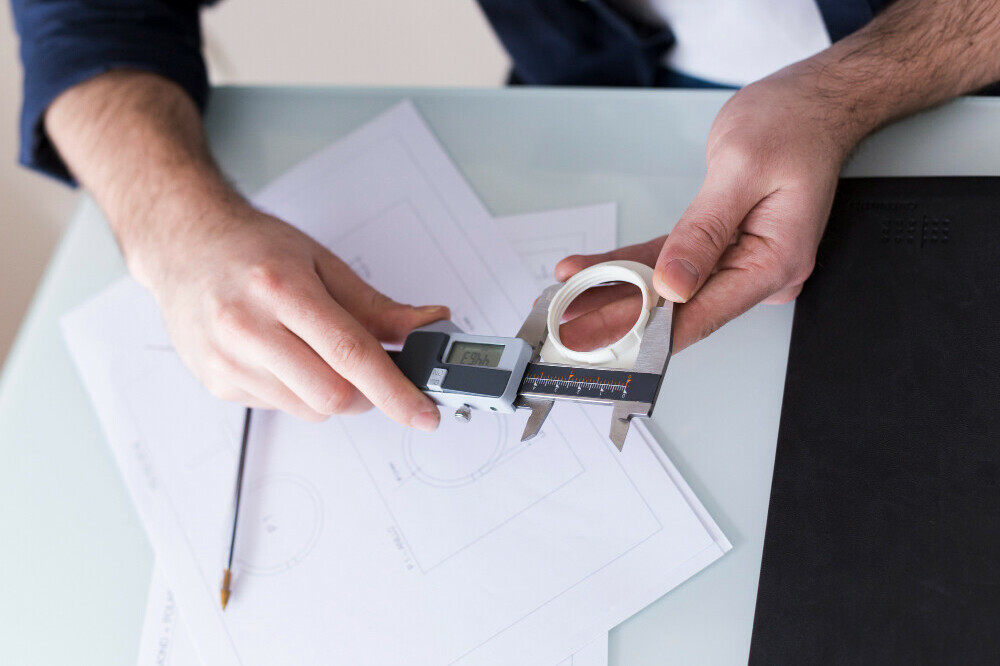
Grasping the core of AS9100 calibration requirements is crucial for aerospace quality management systems. It all starts with ensuring that the equipment used in production and testing meets exacting standards. Each piece of equipment must be capable of producing valid results, which is determined through rigorous calibration.
Calibration, in this context, isn’t a one-off task; it’s an ongoing process that demands comprehensive documentation. Why is this? Because traceability is fundamental. Every step in the calibration process must be recorded: from the personnel who performed the calibration, to the equipment and methods used, to the results and subsequent actions taken.
But the role of documentation doesn’t stop there. It’s vital to develop procedures clearly stating HOW and WHEN calibrations will occur, WHO will perform them, and what STEPS will be taken in the event of equipment falling outside acceptable tolerance levels. Here’s where the consideration of uncertainty comes into play—a factor often overlooked but highly critical.
And there’s a temporal element to it as well—a calibration schedule must be adhered to. The frequency of calibration is not arbitrary; it’s dictated by factors such as the equipment’s usage rate, stability, and purpose. Additionally, after any situation that may have compromised the equipment’s accuracy, recalibration is required.
Lastly, calibration isn’t just about complying with standards; it’s about embedding quality into your operation. When you analyze the calibration results regularly, you can spot trends. Is equipment consistently pushing the boundaries of its tolerance? This could be an early warning sign that something needs attention, enabling proactive maintenance rather than reactive firefighting.
What Are the Prerequisites for Calibration?
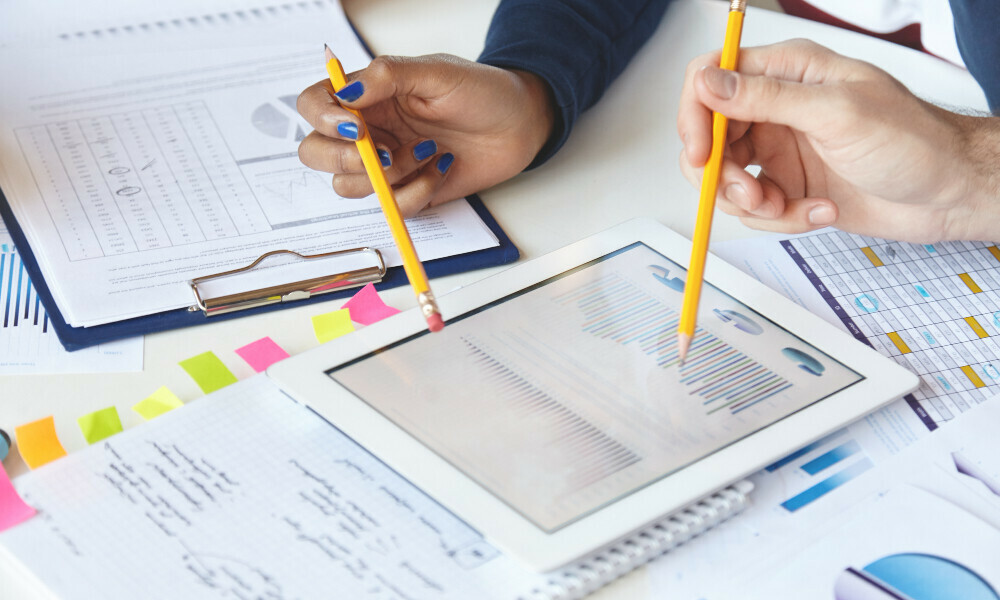
Before diving into the actual calibration process, there are a series of conditions and steps that must be satisfied; I call them prerequisites for calibration. Think of them as the foundation you lay before building a house – they’re absolutely vital for ensuring your calibration efforts stand on solid ground. Addressing these prerequisites is a key element of the AS9100 quality management system. They encompass everything from the surrounding environment where calibration takes place, to the competency of personnel handling the delicate task.
First off, ENVIRONMENTAL CONDITIONS must be controlled. Calibration is sensitive work; temperature and humidity fluctuations can skew results, so they need to be monitored and maintained within permissible limits. Then there’s the question of equipment stability. Before any tool or instrument is deemed ready for calibration, it’s essential to make sure it has been stable in the controlled environment for an adequate ‘settle-in’ period.
Personnel qualifications are equally important. It’s not just a matter of having a warm body in a lab coat; you need individuals who are thoroughly TRAINED and QUALIFIED. That means they have the necessary education, skills, and experience to perform calibrations accurately. This extends to understanding the standards and guidelines that govern their tasks, as well as being able to interpret data correctly and make informed decisions.
Finally, a documented baseline must be established. This involves using reference standards or materials that provide a benchmark against which all measurements can be compared. Having a clear, documented procedure ensures that your calibration work is REPEATABLE AND RELIABLE across different sessions and personnel changes, safeguarding consistency over time.
All these elements form the crux of the AS9100 requirements; they’re non-negotiable and indispensable for a robust calibration process. As we edge closer to the specifics of the ISO guidelines in the next section, keep in mind how the prerequisites mentioned here interlace with the broader context of industry standards and best practices.
What is the ISO Guideline for Calibration?
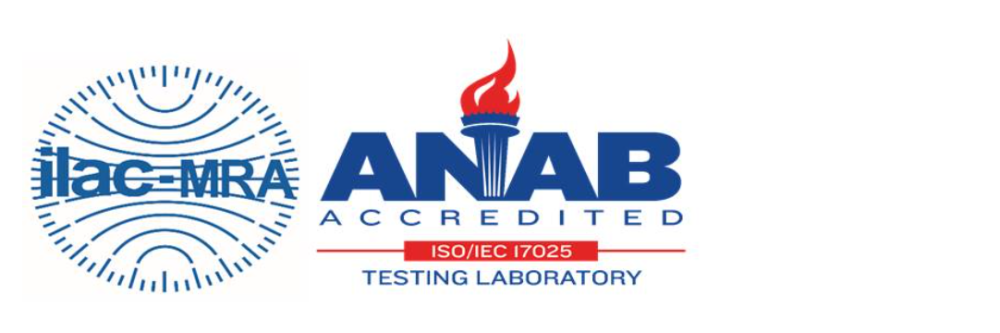
In the realm of calibration, while AS9100 sets the stage for quality management within the aerospace industry, ISO/IEC 17025 plays a pivotal role by defining the general requirements for the competence of testing and calibration laboratories. The ISO 17025 calibration requirements serve as the ISO guideline for calibration, bridging the gap between general quality management practices and the specific technical competencies required for precise calibration. It should also be mentioned that there are ISO 9001 calibration requirements as well.
ISO/IEC 17025 is recognized internationally and applies to all organizations performing laboratory activities, regardless of the industry. It specifies the criteria that laboratories must meet to demonstrate they operate a quality management system, are technically competent, and are able to produce technically valid results. For the aerospace sector, adherence to this standard underscore a commitment to achieving and maintaining high levels of accuracy and reliability in measurement, which is essential for ensuring the safety and performance of aerospace products.
The guideline emphasizes the importance of a laboratory’s ability to consistently produce valid results, outlining requirements for personnel qualifications, equipment calibration and maintenance, and quality assurance of test and calibration data. It encompasses both management requirements, which are related to the operation and effectiveness of the quality management system within the laboratory, and technical requirements, focusing on the competence of staff, methodology, and technology.
Adopting ISO/IEC 17025 within the context of AS9100 calibration activities not only enhances the credibility of the results obtained but also facilitates cooperation between laboratories and other bodies by generating wider acceptance of results between countries. Compliance with this standard signals to aerospace stakeholders that a laboratory operates with integrity, and its findings are based on sound scientific principles, thus instilling confidence in the calibration processes and, by extension, the aerospace products themselves.
Conclusion: Ensuring Precision in Aerospace Quality Management
In the complex and precision-oriented world of aerospace manufacturing, the quality of the calibration process is not just a matter of compliance, but one of SAFETY and EXCELLENCE. Adhering to the AS9100D standards, integrated with the ISO/IEC 17025 guidelines, provides a framework for achieving reliable, accurate, and traceable measurements. Whether a multinational corporation or a small supplier, the obligation to meet these requirements is universal and non-negotiable.
For businesses in the aerospace industry, the commitment to upholding the calibration requirements of AS9100 is a commitment to QUALITY CONTROL and CUSTOMER SATISFACTION. It ensures that products meet not only the technical specifications but also the rigorous expectations of stakeholders and end-users. Remember, a well-calibrated system leads to high-quality outputs, which in turn fosters trust and dependability in the aerospace sector.
In conclusion, continual investment in the right equipment, training of competent personnel, and adherence to established procedures are the keystones of success in calibration. By embracing these principles, companies can establish a robust Quality Management System that not only fulfills the mandates of AS9100 and ISO guidelines but also enhances the integrity, performance, and safety of aerospace products. Let this be the guiding star: PRECISION in calibration equates to PERFECTION in aerospace quality management.
🕒 Book Your Free 45-Minute Consultation
Have questions about ISO/IEC 17025 or ISO 9001 implementation or accreditation? Schedule a free 45-minute consultation with me to discuss your Company or laboratory’s needs and how we can achieve compliance together.
Schedule Your Consultation