As9100 Vs ISO 9001- What are the Differences and Similarities?
I’m going to kick things off by setting the stage for our discussion on two titans of quality management systems: ISO 9001 Vs AS9100. What are the differences and similarities between these two defining standards? You’re going to find out about their roots and why they’ve become cornerstones in the world of quality assurance.
In the grand scheme of manufacturing and service delivery, maintaining quality isn’t just about meeting expectations, it’s also about embedding consistency and boosting customer confidence. That’s where standards like ISO 9001 and AS9100 come into the picture. These aren’t your everyday guidelines; they are meticulously crafted frameworks that companies across the globe lean on to showcase their commitment to quality.
The story of ISO 9001 begins with its birth as an international beacon for quality. Over time, it’s gained recognition as the go-to standard for quality management, regardless of industry. AS9100 swooped in to elevate those expectations specifically for the aerospace sector, which demands an even higher level of safety and precision.
📘 ISO/IEC 17025 Quality Manual Template
Accelerate your lab’s accreditation process with our comprehensive Quality Manual Template, designed to align with ISO/IEC 17025:2017 standards.
- Fully editable and customizable to fit your laboratory’s needs.
- Includes all necessary procedures, forms, and policies.
- Structured to facilitate easy implementation and compliance.
- Developed by experts with extensive ISO/IEC 17025 experience.
With this introduction, I’ve set up a snapshot of what these standards represent. As we move forward, we’ll dive deeper into ISO 9001, unraveling its components, and the breadth of its application in industries far and wide.
Demystifying ISO 9001: The Universal Benchmark for Quality
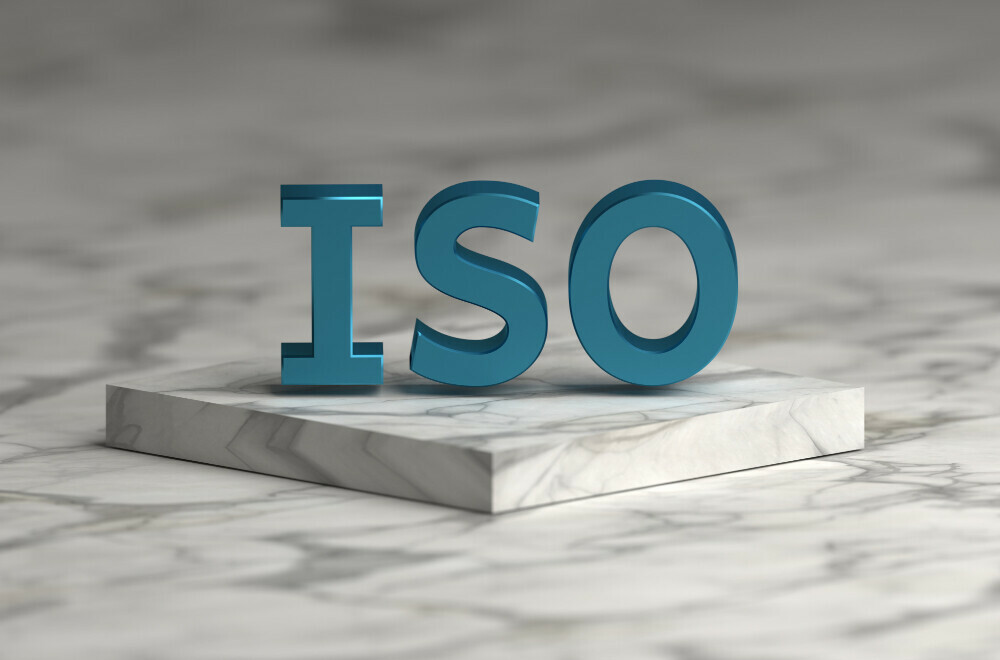
I’m going to break down the ISO 9001 standard, which is the backbone of numerous Quality Management Systems (QMS) across a bevy of industries. It’s crucial to understand that ISO 9001 isn’t an exclusive club for a specific niche; rather, it’s an all-encompassing framework designed to streamline processes, enhance efficiency, and ultimately, ensure customer satisfaction regardless of the sector.
Let’s unpack the core elements. ISO 9001 revolves around a set of principles, including strong customer focus, the involvement of top management, the process approach, and continual improvement. These pillars are not just platitudes but actionable directives that pave the road to quality excellence.
You’re going to find out about how ISO 9001 permeates various industries. Whether it’s manufacturing, healthcare, technology, or services, the ISO 9001 standard is a testament to a company’s commitment to quality. When a company says, ‘We’re ISO 9001 certified,’ they’re proclaiming they have the processes in place to consistently meet customer requirements and regulatory standards.
In my opinion, the real beauty of ISO 9001’s versatility is its scalability. Small start-ups, medium-sized businesses, and large multinationals alike can tailor the ISO 9001 standards to their particular operational scope, offering a common language for quality that meets international benchmarks and facilitates global commerce.
In the next section, I will explain the significance of a specialized offshoot of this universal standard – the AS9100. This adaptation is a game-changer for organizations in the aerospace industry, fortifying the foundational ISO 9001 structure with extra layers of rigor for aviation, space, and defense.
AS9100: Tailoring Excellence for the Skies
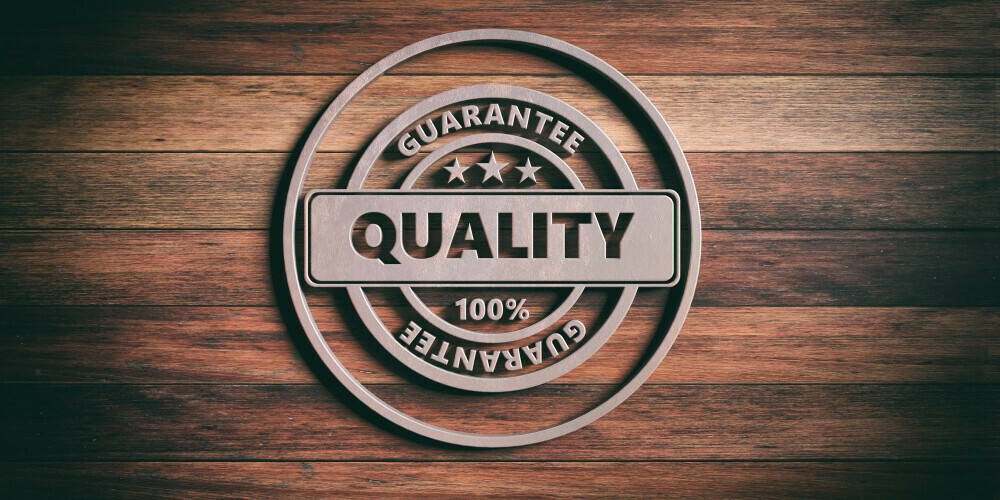
You’re going to find out about the specialized nature of the AS9100 standard, which was crafted to meet the complex, rigorous demands of the aerospace sector. These intricacies go beyond the baseline of ISO 9001 to address the heightened safety, reliability, and quality that aerospace products and services must adhere to.
In my opinion, the necessity of understanding the AS9100 requirements in this industry cannot be overstated. The tight tolerances, extreme environments, and the critical nature of flying machines mean there is minimal room for error. AS9100 supplements ISO 9001 with additional requirements that deal with design, development, and production specifically with these challenges in mind.
Key additions made in AS9100 include risk management, configuration management, and a focus on product safety. Companies are also held to stringent standards regarding counterfeit parts prevention and ethical behavior. These elements are crucial in an industry where even a small component’s failure can have catastrophic consequences.
This isn’t just about adding extra clauses for the sake of complexity; it’s about creating a process that becomes second nature for aerospace companies. A process with the power to significantly reduce risks and drive product and service improvements. Choose something that resonates with you when you think about quality and safety, and you’ll understand the impetus behind AS9100.
A lot is happening very quickly in the field of aerospace. With advancements in technology and growing global demands, the AS9100 standard is increasingly indispensable. It offers comprehensive guidance that helps organizations navigate this fast-paced landscape.
Dissecting the Nuances: AS9100 Vs ISO 9001
Understanding ISO 9001 sets a solid foundation, but it’s not just about what ISO 9001 entails; it’s also about how AS9100 elevates those standards for the aerospace industry. I’m going to walk you through some of the key differentiators that set AS9100 apart.
At first glance, AS9100 may seem like a carbon copy of ISO 9001 with a few aerospace bells and whistles tacked on. Nope. It’s a robust framework designed to meet the critical safety, reliability, and regulatory demands of the aerospace sector. This stems from adding specific requirements to ISO 9001’s risk-based thinking, quality management principles, and process approach.
The differences aren’t just subtle, they’re significant. AS9100 includes additional safety standards; critical aspects of product release; and strict adherence to regulatory compliances specific to aerospace. Suppliers in this field must demonstrate an unyielding commitment to these areas to obtain certification.
Risk management is a particular focal point where AS9100 digs deeper. It goes beyond the ISO 9001 requirements, demanding a more detailed analysis and evaluation of risks throughout the product life cycle. The aerospace standard also dictates thorough documentation, traceability, and consistent quality, which are paramount in the industry.
The contrast extends to counterfeiting prevention and project management. AS9100 addresses the unique challenges of aerospace projects, which can span years and involve numerous stakeholders. ISO 9001, while comprehensive, doesn’t zoom in on these specific industrial requirements.
Before transitioning to the next section, remember that the comparative analysis isn’t about declaring a winner. It’s about articulating how AS9100 extends the ISO 9001 framework to accommodate a specialized field. Choose something that resonates with your industry’s needs for quality and safety.
Ascend to Aerospace: Transitioning to AS9100 from ISO 9001
I’m going to guide you through arguably one of the most exciting phases for a company in the manufacturing sector: transitioning to AS9100 from ISO 9001. This isn’t just about upgrading to a new standard. It’s about aligning with the elite requirements of the aerospace industry.
You’re going to find out about the critical steps involved. First, you must ensure thorough comprehension of AS9100 requirements. This includes getting familiar with the additional aerospace-specific clauses which place a heavier emphasis on product safety and reliability.
Conducting a gap analysis is your second step. It measures the distance between your current quality management system and the lofty heights of AS9100. This practical approach identifies specific areas that need beefing up to pass the stringent scrutiny of an aerospace auditor.
Documentation is, well, monumental here. It’s crucial to meticulously document every process that will be evaluated against AS9100 standards. And, guess what? That’s going to include pretty much everything from design to delivery.
After documentation, you’ll focus on implementation. Training employees, revamping processes, and engaging suppliers who share your commitment to aerospace-quality excellence are all part of this voyage.
Internal audits play a critical role. They act as a dry run for the real thing, providing insights into what’s working and, more importantly, what’s not. They offer you a chance to fine-tune your systems before inviting an official certification body to scrutinize your operations.
The certification audit is the summit of this journey. If you’ve covered all your bases, you’ll exchange your ISO 9001 badge for the coveted AS9100 certification. And this segues beautifully into the benefits of certification…
The Mark of Excellence: Unlocking the Pros of ISO 9001 Vs AS9100
Choosing to certify your organization in ISO 9001 or AS9100 is more than just adhering to quality standards; it’s about committing to a culture of excellence that can have significant ripple effects across your business. Certification isn’t merely a badge to showcase—it’s a proactive stance in quality assurance that screams reliability and trust to your clients and stakeholders.
In my opinion, the advantages of getting your company certified can’t be overstated. For starters, it sets a clear expectation for consistency in your processes, which directly translates to higher customer satisfaction. When you’re distributing products or providing services that meet high standards, customers take notice—and they stick around.
But there’s more. Tremendous opportunity lies in leveraging the competitive edge that comes with certification. In the crowded marketplace, having that ISO 9001 or AS9100 certification can be the differentiator that puts you ahead of the competition. It’s a statement that you don’t just meet the minimum requirements, you thrive on going above and beyond.
And don’t forget about the internal benefits. Streamlining operations and elevating efficiency isn’t something that just
happens—it requires diligent effort and a foundation in proven best practices. These standards give you the blueprint to build upon, fostering continuous improvement and innovation within your teams.
As we wrap up, remember this isn’t just about achieving a certificate to hang on the wall. It’s about embracing a philosophy of quality that permeates every facet of your operations. From customer feedback to internal audits, each aspect of your business can be enhanced with the principles laid out by ISO 9001 and AS9100.
I really hope that you’ve gained a deeper insight into why striving for certification is important and how it places you on the trajectory for stratospheric success. Before you set off on your journey towards quality excellence, take a moment to reflect on the unique needs of your organization and choose the path that resonates most with your goals.
The world is moving quickly; those willing to invest in reliable, high-quality processes and products are going to see the benefits. So if you’re at the crossroads, wondering if certification is worth the effort, I’m here to tell you it is. It’s time for your organization to shine—step into the realm of certified excellence and let your commitment to quality be your guiding star.
🕒 Book Your Free 45-Minute Consultation
Have questions about ISO/IEC 17025 or ISO 9001 implementation or accreditation? Schedule a free 45-minute consultation with me to discuss your Company or laboratory’s needs and how we can achieve compliance together.
Schedule Your Consultation