Root Cause Analysis For Corrective Action
I’m here to help you understand something fundamental yet powerful – the concept of Root Cause Analysis for Corrective Action (RCCA). When things go awry in any business, it’s tempting to slap a quick fix on a problem and move on. However, that’s akin to slapping a band-aid on a broken arm. Sure, it might cover the issue, but it doesn’t resolve the underlying cause. That’s where root cause analysis comes into play. It’s a systematic process designed to dig deep and uncover the actual origins of issues, ensuring that solutions are not just effective, but enduring.
If you’re involved in any industry where quality and efficiency are paramount—and let’s be honest, that’s pretty much every industry—then you’re going to find out about the importance of RCA. The fact of the matter is, if you don’t get to the root cause of the problem, you cannot have an adequate corrective action. Whether it’s manufacturing, healthcare, technology, or services, RCA is the unsung hero behind the scenes, making sure that once a problem is solved, it stays solved.
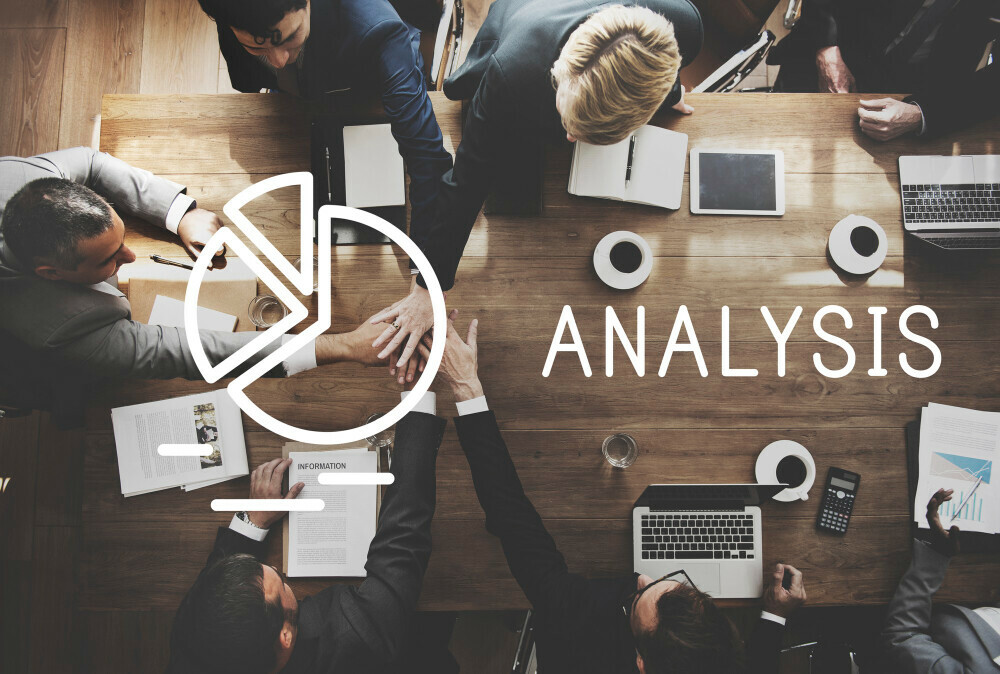
📘 ISO/IEC 17025 Quality Manual Template
Accelerate your lab’s accreditation process with our comprehensive Quality Manual Template, designed to align with ISO/IEC 17025:2017 standards.
- Fully editable and customizable to fit your laboratory’s needs.
- Includes all necessary procedures, forms, and policies.
- Structured to facilitate easy implementation and compliance.
- Developed by experts with extensive ISO/IEC 17025 experience.
Neglecting the root cause of problems can lead to recurring errors, customer dissatisfaction, and even safety hazards. Imagine a scenario where the same issue keeps cropping up; it costs time, resources, and hurts your company’s reputation. RCA is the detective work that stops this vicious cycle by addressing problems at their core. When RCA is done right, the benefits are clear: improved quality, enhanced safety, stronger performance, and ultimately, a healthier bottom line.
In the next section, ‘Understanding RCA: Foundations for Problem-Solving,’ we’re going to dive into the nuts and bolts of RCA. You’ll get acquainted with how RCA stands apart from surface-level troubleshooting and how its proactive nature serves as a preventative measure, safeguarding against future issues. Stay tuned to get your foundation set in the world of Root Cause Analysis.
Understanding Root Cause Analysis for Corrective Action: Foundations for Problem-Solving
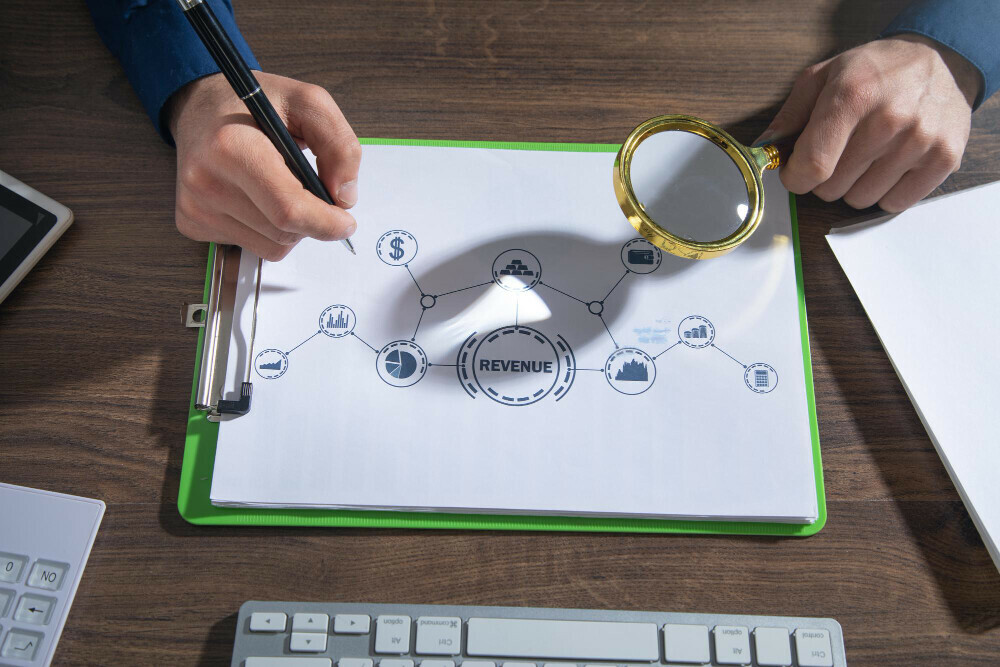
I’m going to walk you through the nuts and bolts of Root Cause Analysis, often abbreviated as RCA. At its core, RCA is more than just a fancy term for troubleshooting; it’s a systematic process designed to get to the bottom of problems and nip them in the bud. Think of RCA as detective work, where you don’t just patch up the leaks, you find out why the pipes burst in the first place.
So, RCA is the methodical approach that targets the underlying issues that contribute to a problem, rather than just addressing the immediate symptoms. It’s about peeling back the layers until you hit the core issue. As a proactive tool, it aims to prevent problems from recurring, saving time, resources, and a lot of headaches down the road.
You’re going to find out about how RCA differs from other problem-solving approaches. While some tactics deal with problems on a surface level, RCA digs deeper. It’s not about the quick fix, it’s about sustainable solutions. That’s why, in my opinion, understanding the difference between symptoms—those are your tell-tale signs that something’s not right—and the actual root cause—the real culprit causing the ruckus—is crucial.
That brings us to the preventive versus reactive debate. A reactive approach scrambles to fix issues after they’ve erupted, often under pressure and in haste. Preventive measures, courtesy of RCA, allow for a more composed and insightful response. This method equips teams with the foresight to anticipate and mitigate issues before they turn into full-blown crises.
This isn’t just about fixing what’s broken today; it’s also about paving the way for a smoother, more efficient future. And the next section will take you through the critical steps of performing RCA—the 10-step process that transforms conventional problem-solving into an art form.
Navigating the RCA Journey: A 10-Step Methodology
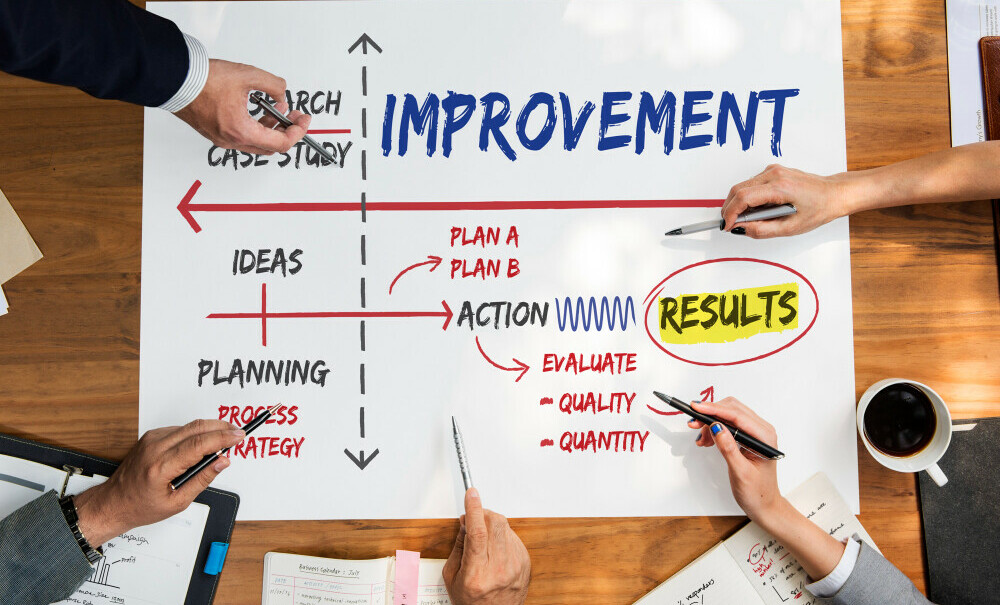
I’m going to walk you through a structured approach to Root Cause Analysis (RCA) that’s as methodical as it is insightful. This 10-step process isn’t just about finding an issue; it’s also about uncovering the underlying problems that lead to failures. It’s a journey from the first hint of a problem to a robust solution that sticks.
- Get the Right Mix of People Involved: Form a cross-functional team to ensure diverse perspectives are included. This collaboration is crucial for considering every angle of the problem and fostering an environment for innovative solutions.
- Define the Problem Clearly: Emphasize the importance of a well-defined problem statement. A precise definition of the issue is essential, as it sets the stage for effective problem-solving.
- Collect Data: Gather relevant data related to the problem. This step is fundamental in understanding the scope and impact of the issue.
- Chart a Sequence of Events: Outline the events leading up to the problem. This chronological mapping is key to identifying potential breakdowns and failure points.
- Identify Potential Causal Factors: Look into factors that might have contributed to the problem. This involves a detailed analysis to uncover possible causes.
- Test the Most Likely Causes: Use the collected data to test hypotheses about the root causes. This scientific approach helps confirm or disprove your theories about what led to the issue.
- Pinpoint the Root Cause: Determine the underlying cause of the problem based on the evidence gathered. This step is critical in ensuring that the solution addresses the core issue. There are several approaches that can help with this process: The 5 why method, cause and effect analysis, and failure mode and effect analysis (FMEA) to name a few.
- Plan Corrective Actions: Develop a strategy for corrective measures that directly target the identified root cause. This plan should aim to rectify the issue and prevent recurrence.
- Implement Corrective Actions: Execute the planned corrective actions. The implementation should be carefully managed to ensure it effectively resolves the problem.
- Update Documentation, Train Relevant Teams, and Monitor the Situation: After implementing changes, it’s important to update any affected documentation, provide training to relevant teams, and continuously monitor the situation to prevent the problem from recurring. This step ensures the solution is sustainable and the issue is truly resolved.
By following these 10 steps in a structured and methodical way, you can perform Root Cause Analysis with diligence, laying the foundation for effective problem-solving and continuous improvement.
Principles of Root Cause Analysis
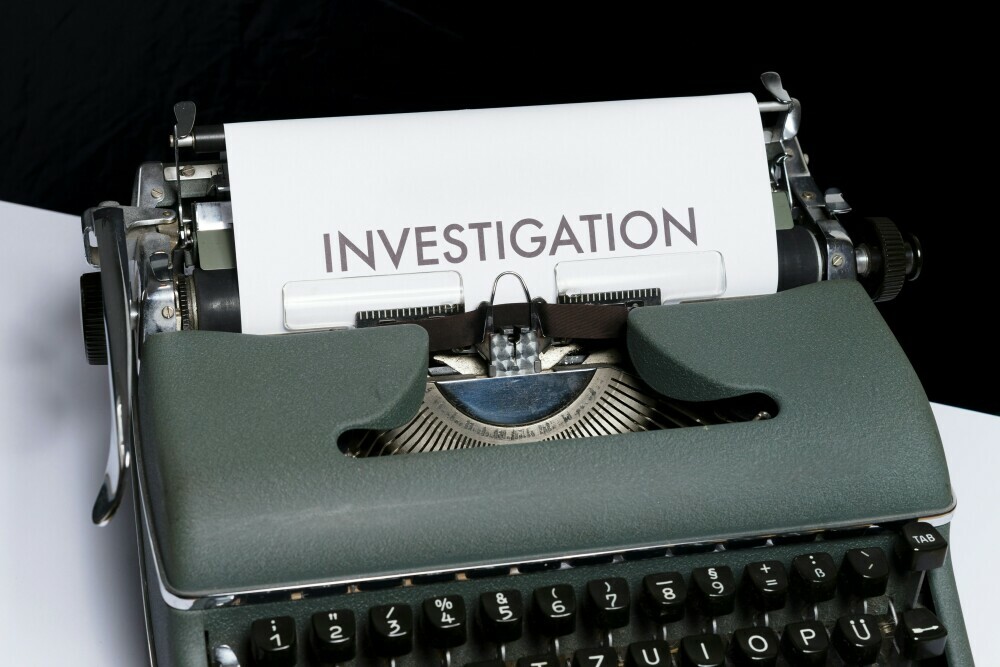
In my opinion, the principles of Root Cause Analysis (RCA) are the bedrock of any investigation. When you understand these principles, you’re going to find out about how they transform your approach to problem-solving from a hit-or-miss venture into a reliable process with predictable outcomes. This isn’t just about fixing problems; it’s also about establishing a culture of continuous improvement.
A standardized approach is like a compass in the wilderness of operational complexities. It ensures that every team member speaks the same language and follows the same map. Fact-based decision making is your safeguard against the minefield of assumptions. By relying on data, you’re less likely to fall prey to intuition, which, while valuable, can sometimes lead us astray.
And don’t worry too much about making mistakes—you can always improve upon your methods. Testing to confirm root causes is a vital step, and I’d recommend you consider it as essential as a detective confirming an alibi. You’re building a case for a solution, and that foundation needs to be rock solid. Otherwise, the slightest tremor of uncertainty could bring the whole structure crashing down.
Finally, implementing permanent corrective solutions is the zenith of RCA. Choose something that resonates with you and your team’s goals and values, something durable and adaptable. Because here’s the thing: the goal isn’t just to slap a quick fix on the problem or to correct a deviation from nonconforming work. You’re aiming for solutions that reshape the way you operate for the better, long into the future.
Root Cause Analysis for Corrective Action – Video
A great way to get a clear understanding of how root cause analysis for corrective action works is to get the inside scoop from an ISO certification body. These are the people who audit your corrective action process and thus can offer firsthand advice. I cannot think of a better source that from Perry Johnson Registrars to get a detailed look into how root cause analysis for corrective action works, watch the video below:
Precision in Practice: 3 Tools You Can Use for Root Cause Analysis
Root Cause Analysis (RCA) is a cornerstone of problem-solving and quality improvement efforts, offering tools and techniques to identify the underlying causes of problems. Among the most effective RCA techniques are the 5 Whys, Cause and Effect Analysis, and Failure Mode and Effects Analysis (FMEA).
The 5 Whys technique
is straightforward yet powerful, involving the iterative questioning of why a problem exists. By asking “Why?” five times (or as many as needed), it peels away the layers of symptoms to reveal the root cause. This method, ideal for simple to moderately complex issues, emphasizes a deeper understanding of the problem at hand.
Cause and Effect Analysis,
also known as Fishbone or Ishikawa Diagram, visually maps out the various causes leading to a problem. It categorizes potential causes into different buckets such as methods, machinery, people, materials, measurement, and environment, allowing teams to systematically explore and pinpoint where issues may originate. This technique is particularly useful for complex problems where multiple factors might be at play.
Failure Mode and Effects Analysis (FMEA)
is a more structured and comprehensive approach, identifying potential failure modes, their causes, and effects on system operations. By assessing the severity, occurrence, and detection of failures, FMEA helps prioritize risk and guide actions to mitigate those risks. It’s especially valuable in manufacturing and product development for preventing future quality issues.
Incorporating these RCA techniques into problem-solving processes ensures a thorough analysis, leading to more effective and sustainable solutions. By choosing the appropriate method based on the complexity and nature of the problem, organizations can significantly improve their troubleshooting capabilities and overall operational efficiency.
For a more detailed exploration of each technique, including practical examples and step-by-step guides, you may consider looking directly into specialized resources or training materials dedicated to RCA methodologies.
Conclusion: RCA – Root Cause Analysis for Corrective Action
In wrapping up, it’s clear that Root Cause Analysis for corrective action isn’t just a one-off exercise; it’s a cornerstone of enduring improvement in every industry. By thoroughly investigating the underlying reasons for issues, organizations can move beyond temporary fixes and develop robust solutions that prevent recurrence.
I’ve walked you through what RCA entails, its structured approach, and the tools that power it. While challenges such as biases and complex data can arise, the strategies we’ve discussed are your roadmap to overcoming these hurdles effectively.
The real magic happens when RCA transforms from concept to practice, with dedication and precision. You’ve seen through the lens of Lockheed Martin and various case studies how impactful a diligent RCA process can be.
So remember, if you’re aiming for long-term success in quality, safety, or operational efficiency, embedding RCA into your organization’s culture isn’t optional, it’s essential. Choose something that resonates with you, integrate it into your processes, and watch as the benefits unfold.
Your first attempt at RCA doesn’t need to be perfect. You can always adjust your approach down the road, refining your methods as you gain more insight. And I really hope that you do because the potential for growth and excellence is immense.
Thanks for accompanying me on this journey through RCA. Keep pushing for those root causes, and soon, you’ll see improvements that are not just effective, but transformational.
🕒 Book Your Free 45-Minute Consultation
Have questions about ISO/IEC 17025 or ISO 9001 implementation or accreditation? Schedule a free 45-minute consultation with me to discuss your Company or laboratory’s needs and how we can achieve compliance together.
Schedule Your Consultation