8 Steps to Implementing a QMS: Your Roadmap to Quality Management Success
Implementing a Quality Management System (QMS) can be a transformative step for organizations aiming to enhance their efficiency and product quality. With a well-structured QMS, companies can better manage their processes, improve customer satisfaction, and ensure compliance with industry standards. Embarking on a QMS implementation requires a thorough understanding of the company’s objectives and a strategic alignment with its processes and resources. Here are 8 steps to implementing a QMS.
The journey towards QMS implementation is systematic and demands meticulous planning and execution. It starts with defining and mapping out critical processes that affect product quality and customer satisfaction. A clear quality policy sets the direction for the organization, while specific, measurable quality objectives align with business goals. Throughout the process, training and communication are paramount in ensuring that staff are aware of their roles within the QMS and are committed to its success.
Key Takeaways
- A robust QMS aligns organizational processes with quality objectives.
- Training and effective communication are crucial to successful QMS adoption.
- Continuous review and improvement are at the heart of QMS effectiveness.
Define and Map Your Processes
In laying the groundwork for a robust Quality Management System (QMS), my first focus is to define and map out all critical processes. This ensures clarity and cohesion, which are instrumental in maintaining operational efficiency and meeting my planning objectives. It is important to consider utilizing the plan-do-check-act (PDCA) cycle which allows for continuous improvement to both your product and your overall QMS.
📘 ISO/IEC 17025 Quality Manual Template
Accelerate your lab’s accreditation process with our comprehensive Quality Manual Template, designed to align with ISO/IEC 17025:2017 standards.
- Fully editable and customizable to fit your laboratory’s needs.
- Includes all necessary procedures, forms, and policies.
- Structured to facilitate easy implementation and compliance.
- Developed by experts with extensive ISO/IEC 17025 experience.
Create Process Flowcharts
I always begin by creating comprehensive process flowcharts. These visual representations serve as a crucial tool for detailing every step within my business operations. My process maps explicitly chart the workflows, making the transition from one step to the next transparent and observable. I emphasize on the following steps to develop my flowcharts:
- Identify Every Process: I list all processes relevant to my operations. Ranging from customer service protocols to product development, no process is too small to be overlooked.
- Delineate Process Boundaries: For every process, I define where it starts and where it ends. This helps me understand the scope and impact of each process within my overall QMS.
- Determine Process Sequences and Interactions: Processes often interact or follow a sequence. I map these relationships to ensure that they are well-coordinated and that I create value at each stage.
- Assign Responsibilities: Every step in the flowchart is assigned a responsible party or department, making accountability a transparent element of my workflows.
- Analyze and Optimize: With my processes mapped, I analyze them for efficiency and potential improvement. Where necessary, I make adjustments to streamline operations and eliminate redundancies.
Through these flowcharts, I secure a clear, systematic visualization of my business processes, anchoring my QMS on a foundation that promotes consistency and facilitates continuous improvement.
Define Your Quality Policy
The foundation of a Quality Management System (QMS) is a well-defined Quality Policy. My policy sets the stage for procedures and objectives, driving my commitment to quality and meeting customer and regulatory benchmarks.
Reflect Commitment to Quality
I articulate my commitment to quality by ensuring that the Quality Policy is a clear expression of my organization’s core values and dedication to excellence. This policy serves as a pledge to continuous improvement and customer satisfaction, acting as the guiding principle for all internal processes and decisions. It is both a promise to my stakeholders and a roadmap that informs the behavior and direction of my team.
Ensure Compliance with Customer and Regulatory Requirements
My Quality Policy is crafted to align with customer needs and regulatory frameworks. To achieve this, I:
- Identify Regulatory Standards: I list the relevant regulations that affect my products or services, ensuring my policy encompasses these essential parameters.
- Match Customer Expectations: I gather data on what my customers expect in terms of quality, making it an integral part of my policy.
- Formalize Compliance Measures: I translate these standards and expectations into specific compliance measures within my QMS, detailing how my policy will uphold quality benchmarks and stipulate methods for monitoring compliance.
Define Your Quality Objectives
When I approach Quality Management System (QMS) implementation, my priority is to define clear and precise quality objectives which are crucial for bolstering organizational goals and ensuring the continuous improvement of processes and products. It is critical that these quality objectives are measurable, and the company is willing to do what it takes to reach their target goals. You also want to make sure these objectives are reachable, but not to easy to ensure you are driving improvement to your processes.
Set Measurable Goals
Objectives: I identify what constitutes success for my organization by setting specific and measurable goals. It is crucial that these goals are quantifiable to track my progress and make adjustments as necessary.
- Specificity: I ensure that each objective is clear and unambiguous.
- Measurability: I incorporate quantifiable targets that allow me to track the improvements using Key Performance Indicators (KPIs).
- Timeliness: I set a realistic timeframe to achieve my objectives to maintain momentum and focus.
Align with Quality Policy
Alignment: My quality objectives are always in tune with the broader quality policy of the organization, supporting its mission and vision. In fact, I always put the aspirational statements of a section of the quality policy in a column right next to the particular quality objective that I document on a quality objective register. See example below.
- Consistency: I make certain that my goals support and reinforce the quality policy, avoiding any conflicts or discrepancies.
- Organizational Goals: I take into account the overarching organizational goals to ensure that achieving my quality objectives contributes to the larger business outcomes.
By staying aligned with my quality policy and ensuring my objectives are measurable, I lay a sound foundation for a QMS that drives my organization towards excellence. Notice that there is a CAR column in the example below. This is used internally to drive improvement. It is an example how to use the corrective action process to drive improvement.
Since quality objectives are internally created, the organization is setting the parameters themselves. This is an excellent way to drive improvement and force the organization to reach its goals. This is why it is important to set achievable goals, but do stretch yourselves a bit as well.
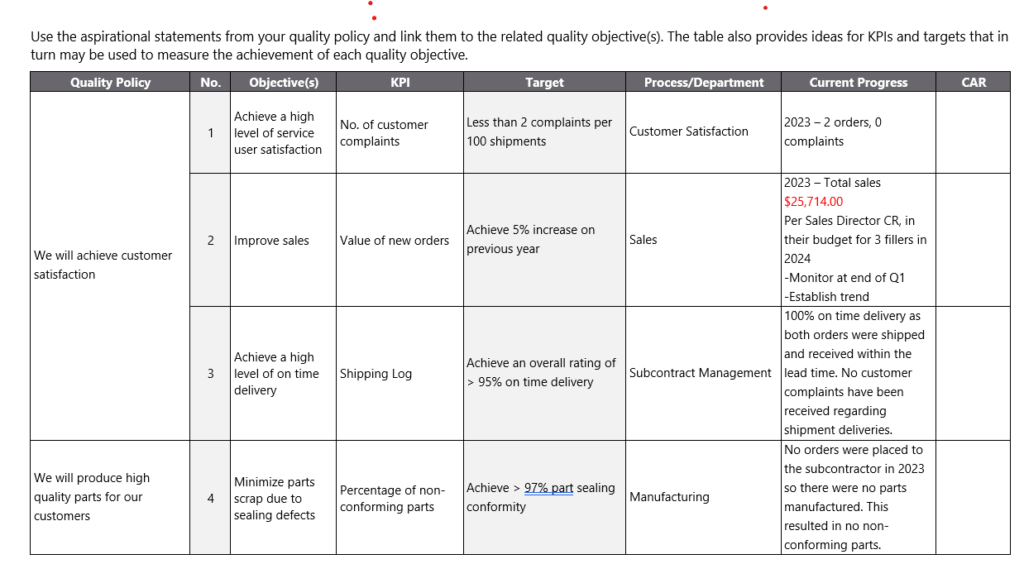
Develop Metrics to Track and Monitor CSFs
Developing precise metrics is essential for tracking and monitoring Critical Success Factors (CSFs) within a Quality Management System (QMS). I will outline how to pinpoint the most impactful metrics to measure performance effectively.
Identify Critical Metrics
The initial step in ensuring my QMS’s effectiveness is to identify key performance indicators (KPIs) that align directly with CSFs. These metrics should be quantifiable, relevant to my organization’s goals, and provide clear indications of performance. Here’s how I approach this:
- Quantification: I translate CSFs into specific, measurable KPIs. For instance, if customer satisfaction is a CSF, I might measure it using net promoter scores or customer satisfaction ratings.
- Relevance: The chosen metrics must reflect those processes and outcomes that critically impact my organization’s strategic objectives.
- Benchmarking: I establish benchmarks for each KPI, which involve setting targets based on industry standards or my historical data, to track improvements over time.
- Data Collection Process: I set up a robust process to collect data methodically. This means determining who will collect the data, how frequently, and through which methods or tools.
- Regular Reviews: I schedule frequent reviews of these KPIs to ensure they are still aligned with my QMS goals and make adjustments as necessary based on findings from the data collected.
Carry Out an Internal Organization QMS Audit
To ensure that a Quality Management System (QMS) is effective and aligns with the standards such as ISO 9001:2015, ISO/IEC 17025, or to what is ISO 17020, I must conduct internal audits routinely. This process allows me to assess compliance, identify gaps, and maintain certification through a systematic review of our processes and procedures.
Assess Current State of QMS
The first step I take during an internal audit is to thoroughly assess the current state of our QMS. This involves:
- Document Review: I evaluate all relevant QMS documentation against the ISO 9001:2015 standards to ensure that what is on paper is up to the mark.
- Process Observation: I observe the processes in action, ensuring they match the documented procedures.
- Employee Interviews: I conduct interviews with employees to verify their understanding and implementation of the QMS guidelines.
By doing so, I can confirm the degree of compliance with the established QMS and ensure that it supports our business objectives effectively.
Identify Gaps
After assessing the current state, the next step is to identify any discrepancies between our practices and QMS requirements. I perform a gap analysis, which includes:
- Gap Identification: Listing out areas where our practices do not meet the requirements specified by the QMS or the ISO 9001:2015 standard.
- Risk Evaluation: Assessing the potential impacts of these gaps on our operations, quality output, and customer satisfaction.
- Action Plan: Drafting a detailed action plan to address these gaps in a prioritized manner, ensuring timely compliance and continuous improvement.
The gap analysis not only helps me spot non-conformities and potential areas of improvement, but also plays a crucial role in preparing for external audits and maintaining QMS certification.
Document Your Processes and Procedures
In implementing a Quality Management System (QMS), I ensure the documentation of all processes and procedures. This is a crucial stride towards standardization and accountability, laying the groundwork for a culture of quality and continuous improvement.
Maintain Consistency
To maintain consistency, I develop documentation standards that serve as a uniform baseline. This often includes:
- Structured formats for different document types (e.g., procedure manuals, work instructions).
- Use of controlled documents to prevent unauthorized changes.
- A document hierarchy that clearly defines the importance and interrelation of documents.
Here is an example of a simple document control table:
Document Type | Description | Control Method | Review Cycle |
---|---|---|---|
Quality Manual | Overarching QMS document | Approval by Quality Manager | Annually |
SOPs | Standard Operating Procedures | Approval through electronic signature | Biannually |
Work Instructions | Step-by-step guides | Regular updates only by authorized personnel | Quarterly |
Records | Evidence of compliance | Storage in secure, organized system | As required by regulations |
Facilitate Effective Training
Properly documented procedures and work instructions are key resources in training employees. By having clear, accessible documentation, I:
- Ensure best practices are taught uniformly.
- Provide a reference that employees can use to reinforce learning.
- Decrease the likelihood of errors or deviations in process execution.
Storage and retrieval of these documents are made efficient through a well-maintained QMS, allowing for swift access to the latest instructions whenever my team needs them.
Train and Communicate with Your Staff

In ensuring the successful implementation of a Quality Management System (QMS), I recognize that effectively training and communicating with staff are critical steps. My staff needs to understand their roles within the QMS and stay updated on any process changes to ensure efficiency and continual improvement.
Understand Roles in QMS
My responsibility is to ensure that each member of my team understands their specific role within the QMS framework. This clarity is achieved through:
- Role-specific training programs: I develop and execute targeted training programs tailored to the unique functions of different roles.
- Support Systems: I establish clear support channels for staff to seek clarification and guidance on QMS-related activities.
My Training Program Structure
Role in QMS | Training Focus | Support Provided |
---|---|---|
Quality Manager | Overseeing QMS implementation and maintenance | Direct line to top management |
Process Operator | Adhering to standard operating procedures (SOPs) | Regular workshops and Q&A sessions |
Sales Personnel | Understanding quality policies’ impact on sales | Access to quality assurance documentation |
Update on Process Changes
When there are changes in our QMS processes, I ensure that all staff members are promptly informed. This communication strategy involves:
- Announcements: Immediate notifications about alterations via company-wide emails or meetings.
- Training Opportunities: Additional training sessions are scheduled to address the knowledge gaps brought about by the updates.
I monitor the incorporation of these changes to gauge understanding and the need for further support or additional trainings. The objective is to maintain a high level of awareness and adaptability among my team members, which ultimately contributes to the continuous improvement of our quality management efforts.
Review and Improve Continuously
Implementing a Quality Management System (QMS) is an ongoing process that requires a commitment to continuous improvement. The goal is not only to maintain quality standards but to elevate them consistently over time.
Utilize Metrics and Audit Data
I rely heavily on concrete data to track the performance and effectiveness of the QMS. Metrics are indispensable because they provide quantifiable measures of quality, and I use audit data to uncover discrepancies or areas in need of enhancement. Together, they inform my continuous quality improvement (CQI) efforts. The following are key components of the data utilization process:
- Key Performance Indicators (KPIs): I establish KPIs that tie directly to quality objectives.
- Regular Audits: I schedule regular audits to assess compliance and identify opportunities for improvement.
- Feedback Loops: I implement feedback mechanisms to capture data from every relevant source, including customer feedback, process outputs, and employee insights.
Make Informed Improvement Decisions
Informed decision-making is central to the CQI process. By analyzing the data collected, I am able to prioritize improvement plans based on their potential impact on the effectiveness of the QMS. The steps I follow include:
- Data Review: I meticulously review all collected data to identify trends and patterns.
- Root Cause Analysis: When issues are identified, I conduct root cause analysis to understand the underlying factors.
- Action Plans: Based on this analysis, I formulate actionable improvement plans with clear objectives and timelines.
- Implementation: I oversee the careful implementation of these plans, ensuring they are executed as intended.
- Evaluation: Post-implementation, I evaluate the outcomes to measure the success of each improvement against the established KPIs.
By incorporating these practice into my routine, I foster an environment of continuous quality improvement that keeps the QMS dynamic and effective.
Frequently Asked Questions
In this section, I’ll address common queries related to the implementation of a Quality Management System (QMS), providing insights for a seamless transition to a structured approach for achieving quality objectives in your organization.
How can an organization develop a comprehensive QMS implementation plan?
To develop a comprehensive QMS implementation plan, I first define clear quality objectives aligned with the organizational goals. Then, I conduct a gap analysis to assess current processes against the desired quality standards, leading to a detailed plan that outlines responsibilities, timelines, resource allocations, and a roadmap for procedural changes.
What are the critical elements to include in a quality management system?
Critical elements that I include in a QMS are a clear quality policy, well-defined processes and procedures that align with industry standards, such as ISO 9001, comprehensive documentation, robust training programs, internal audit mechanisms, and a system for continual improvement that captures feedback and performance metrics.
What strategies are effective for ensuring staff engagement during QMS deployment?
To ensure staff engagement, I utilize clear communication of the benefits and changes the QMS will bring. I also involve team members across various departments in the planning and implementation process, provide appropriate training, and establish recognition programs that reward adherence to QMS processes and quality improvement initiatives.
What are common challenges faced during the QMS implementation process and how can they be overcome?
Common challenges include resistance to change, inadequate resources, and lack of clarity among staff regarding new processes. To overcome these, I focus on strong leadership, ongoing training and support, clear communication, and phased implementation that allows gradual adaptation to the new system.
In what ways can the effectiveness of a newly implemented QMS be measured and sustained?
To measure and sustain the effectiveness of a QMS, I establish key performance indicators (KPIs) relevant to quality objectives, conduct regular internal and external audits, and engage in continuous monitoring and review of processes. I also remain open to feedback and make periodic adjustments to maintain alignment with organizational goals and compliance standards.
Steps to Implementing a QMS – Conclusion
The journey to implementing a QMS is a strategic endeavor that can significantly enhance the quality and consistency of your products and services. By following the outlined steps—starting with a thorough understanding of your current processes, gaining leadership commitment, and engaging your team, all the way through to continuous improvement—you lay down a robust foundation for a system that not only complies with ISO 9001 standards but also aligns with your organization’s unique goals. Remember, the key to a successful QMS is not just in its design but in its execution and ongoing management.
As you move forward, keep in mind the importance of documenting your processes, providing adequate training, and establishing clear lines of communication across your organization. The effort you put into monitoring and reviewing your system will pay dividends in customer satisfaction and operational excellence. Embrace the culture of quality, and let it steer your business practices; after all, quality is not a destination but a continuous journey.
Finally, never underestimate the value of feedback—both internal and external—as it is the compass that guides your QMS towards effectiveness and relevance. By systematically addressing non-conformities and capitalizing on opportunities for improvement, your QMS will not only ensure compliance but will also drive innovation and growth. Keep striving for excellence, and let your commitment to quality shine through every aspect of your business.
🕒 Book Your Free 45-Minute Consultation
Have questions about ISO/IEC 17025 or ISO 9001 implementation or accreditation? Schedule a free 45-minute consultation with me to discuss your Company or laboratory’s needs and how we can achieve compliance together.
Schedule Your Consultation