What Is A Quality Management System – Definition?
You might be asking yourself, exactly what is a Quality Management System – Definition. Simply put, it’s the backbone of a company’s operations, ensuring that quality isn’t something you just talk about, it’s something you live by every single day. Think of a QMS as the central nervous system of an organization’s drive to deliver products or services that consistently hit the mark on customer satisfaction.
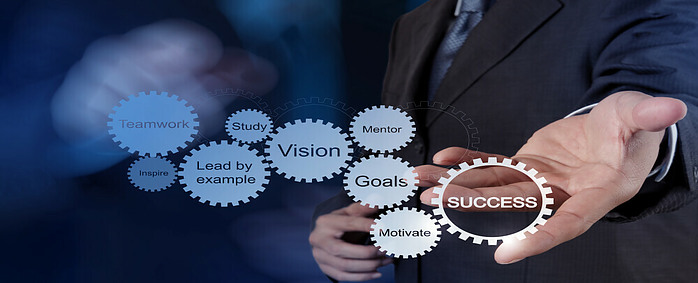
QMS isn’t a new kid on the block. Over the years, it has evolved significantly, tracing its roots back to when quality control meant simply checking products for faults. Now, it’s about a holistic approach entwined with the very fabric of an organization’s culture. By embedding quality into every layer of business activity, companies can not only meet but exceed, customer expectations.
📘 ISO/IEC 17025 Quality Manual Template
Accelerate your lab’s accreditation process with our comprehensive Quality Manual Template, designed to align with ISO/IEC 17025:2017 standards.
- Fully editable and customizable to fit your laboratory’s needs.
- Includes all necessary procedures, forms, and policies.
- Structured to facilitate easy implementation and compliance.
- Developed by experts with extensive ISO/IEC 17025 experience.
This isn’t just about avoiding errors or making something ‘good enough.’ A QMS is about setting up a structured, systematic process that covers everything from your initial concept to the final delivery. It’s about making sure that everyone in the organization understands their role in achieving and maintaining quality, in staying compliant with regulations, and driving continual improvement.
Core Elements and Framework of a QMS
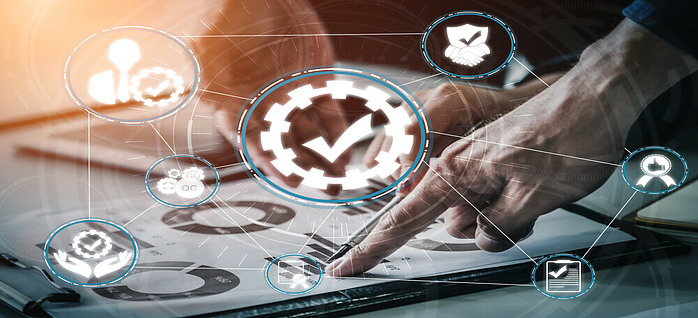
At its heart, a QMS is built upon a few foundational pillars that ensure its robustness and reliability. You’re going to find out about the four essential components that comprise the backbone of any quality management system:
- Process Managment – is the cornerstone of a QMS, focusing on the processes involved in meeting quality objectives. It’s about understanding and mapping out each step that takes a product or service from conception to delivery, ensuring they’re optimized for quality assurance.
- Documentation – this may not be the most glamorous part of a QMS, but it’s vital. This includes clear recording of processes, policies, and procedures. Good documentation is essential for both consistency in operations and as evidence of compliance with the quality standards.
- Quality Policy — Every QMS has one and it is a formal statement from management, closely aligned with the business strategy, that sets the quality objectives and commitments. It acts as a guiding star for the organization’s quality initiatives, and as much as it’s strategic, it’s also about communication. The Quality Policy is considered a top-level document the initiates the foundation of the QMS.
- Quality Objectives – which are the measurable goals that arise from the quality policy. They provide a target for the organization to aim for, focus efforts, and facilitate performance measurement. These quality objectives should consider the quality policy, and somehow tie into them. In fact, this is an ISO 9001:2015 requirement. We will discuss this a little later on.
The implementation of these elements isn’t just about ticking boxes; it’s about weaving them into the organizational fabric. A robust QMS is dynamic, allowing for regular reviews and feedback that lead to continuous improvement. This adaptability is crucial because it ensures the system keeps pace with changes both internally and in the market. It is also a very important step in improving processes at the core.
With these elements in place, a QMS framework provides a blueprint for achieving consistently high-quality outcomes that satisfy customer needs and comply with regulations. Think of it as not just a safety net, but as a trampoline for leaping towards better practices and higher standards.
Interpreting the ISO Standard and QMS
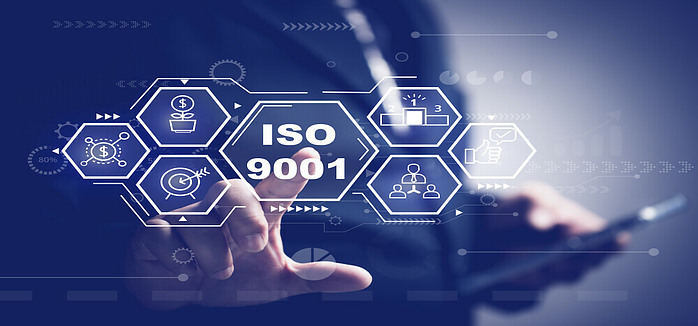
In my experience, the ISO 9001:2015 standard is the linchpin of any robust Quality Management System. It’s not just a set of parameters but a guiding philosophy that emphasizes the importance of meeting customer expectations and regulatory requirements, enhancing customer satisfaction, and continuously improving process efficiency. Whether you organization manufactures widgets, or provides a service, the ISO 9001:2015 standard can apply and can also help you improve your company’s overall performance.
There are other ISO standards that contribute to a quality management system, in fact, there are hundreds of ISO standards that contribute to a quality management system. Another ISO standard that deserves attention is ISO/IEC 17025. What is ISO 17025 accreditation? This is an accreditation standard for the competency of testing and calibration laboratories.
Understanding the ISO standard isn’t just about acquiring a certification or accreditation; it’s about imbibing a culture that fosters quality at every step. When I say ‘ISO definition of QMS’, think of it as a blueprint that affects all aspects of an organization, from the boardroom to the production floor. It outlines the necessity for a process-oriented approach and insists on documented evidence of compliance, planning, and operational prowess.
Now, let’s be clear: When people refer to ‘ISO standards’, they usually mean the documents and requirements that comprise the Quality Management System. However, there’s a distinction to be made. Those documents are reflective of the system, but the QMS is the totality of the operational processes and mindsets geared towards quality within a company.
So why is this such a big deal? Companies that align their QMS with ISO 9001:2015 show they’re serious about quality. They can confidently assure their customers that they have structured, repeatable, and scalable processes to deliver consistent value. And I can’t stress enough how that kind of reliability can elevate business reputation and customer loyalty.
Real-world Applications and Examples of QMS
You’re going to find out about how QMS isn’t just a theoretical concept—it’s a practical, vital strategy used by organizations across the globe. This is where we see the theory put into action and witness the tangible benefits that a robust quality management system can offer.
One of the best ways to understand QMS in practice is by looking at real-world examples. Industries like automotive, healthcare, and manufacturing have long embraced QMS, tailoring it to fit their unique needs and regulatory demands. For instance, in the automotive sector, a QMS ensures consistency in the production of vehicles, contributing to safety and reliability that customers depend on.
But it’s not only about compliance and meeting customer expectations. An effective QMS can elevate a business’s performance by refining processes, reducing waste, and fostering a culture of continuous improvement. Companies such as Toyota have attributed their success in part to their quality management practices—which, yes, include QMS—manifested through their famous ‘Toyota Production System’.
Integrating a QMS also means keeping a finger on the pulse of what customers need and expect. By continually assessing and improving services or products, businesses stay ahead of their competition and often discover new opportunities for innovation and growth.
A QMS is also pivotal in upholding standards when it comes to international trade and globalization. For many industries, having a certified QMS is a prerequisite for entering global markets, ensuring the consistent quality of goods and services from one country to another.
As we transition to the next section, remember that implementing a QMS is a strategic decision that can transform all aspects of an organization’s operations and culture. This bridges us to our next topic: addressing common questions and exploring insights from the American Society for Quality (ASQ), including their perspective on QMS, which plays a significant role in shaping industry standards and practices.
Clarifying Common QMS Questions and the ASQ Perspective
You’re probably starting to see that a Quality Management System (QMS) is a pretty big deal. It’s not just a set of documents or an ISO standard; it’s a comprehensive approach to ensuring quality is baked into every aspect of an organization. When you look closely, it becomes clear why QMS is so essential for meeting customer expectations and regulatory demands, as well as for carving out a competitive edge.
So, what’s the scoop on all those questions you hear flying around about QMS? Well, it’s fairly straightforward. Let’s dive into answering some of the frequently asked questions regarding this fascinating subject.
Frequently Asked Questions
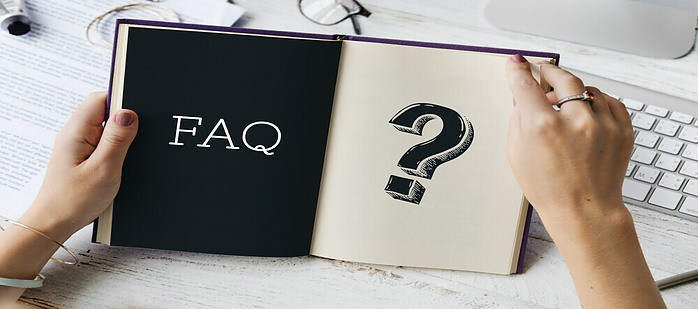
What is a Quality Management System (QMS)?
A Quality Management System (QMS) is a systematic framework designed to manage an organization’s processes, procedures, and responsibilities to achieve quality objectives. It ensures quality is integrated into every aspect of an organization, helping to meet customer expectations and regulatory demands, while also providing a competitive edge.
What are the four elements of a great QMS?
The four elements of a great QMS are Process Management, Documentation, Quality Policy, and Quality Objectives. These elements serve as guiding principles to lead an organization toward consistency and continual improvement.
How does ISO 9001:2015 relate to a QMS?
ISO 9001:2015 provides a clear blueprint for crafting a QMS that is durable and adaptable. It’s not just a certification to achieve; it’s about incorporating a quality mindset into the very culture of an organization.
Can you give examples of QMS in different organizations?
Examples of QMS vary widely, from a small tech startup’s agile approach to a multinational corporation’s extensive system. Regardless of size or industry, all QMS share a commitment to quality, customer satisfaction, and continuous improvement, tailored to an organization’s unique needs.
What is the difference between QA and QMS?
Quality Assurance (QA) focuses on ensuring the quality of products or services through specific activities and checks. QMS, on the other hand, is the comprehensive system that encompasses QA and all other components necessary to maintain quality across an organization.
What is the ASQ’s perspective on QMS?
The American Society for Quality (ASQ) defines a QMS as a driver of organizational effectiveness and efficiency, contributing to continuous improvement. It’s an essential tool for any business serious about quality.
Why is it important to have a QMS in today’s fast-paced world?
In today’s fast-paced world, a solid QMS is foundational, supporting all aspects of an organization from product development to customer service. It’s a strategic backbone that guides an organization towards excellence and allows for continuous learning and adaptation. Quality is a continuous journey, not just a destination.
Conclusion
So, what Is a Quality Management System Definition?
In conclusion, a Quality Management System (QMS) is a critical component of an organization, ensuring that quality is a tangible aspect of operations. It represents an organization’s dedication to excellence, aiming to exceed customer expectations and emphasizing the importance of continuous improvement. A QMS evolves with the organization, transforming from a basic defect-prevention tool into a strategic framework that integrates Process Management, Documentation, Quality Policy, and Quality Objectives to enhance operational efficiency and embed a proactive quality mindset throughout the company.
Embracing a QMS signifies a commitment to constant improvement and ingrains a culture of quality within the company’s core. It narrates a tale of excellence that resonates with the reliability and trust customers place in the company’s products and services. This approach not only meets but sets new benchmarks for quality, ensuring the company’s legacy endures through changing markets and rigorous global standards. Read this article if you are interested in learning more about the purpose of a quality management system.
Looking forward, the implementation of a QMS should be seen as an opportunity to revolutionize an organization’s essence. It’s not just a step but a significant leap toward a future where quality is exceptionally guaranteed. The QMS is not a static set of rules but a living system that drives progress, urging us to embark on this path with vision, openness, and the understanding that the journey toward quality excellence is perpetual, with every step fortifying a legacy of value and customer trust.
🕒 Book Your Free 45-Minute Consultation
Have questions about ISO/IEC 17025 or ISO 9001 implementation or accreditation? Schedule a free 45-minute consultation with me to discuss your Company or laboratory’s needs and how we can achieve compliance together.
Schedule Your Consultation