Understanding The ISO 9001 Standard: Fundamentals of Quality Management Systems
Understanding the ISO 9001 Standard begins with recognizing its role as a pivotal international standard that outlines the criteria for an effective quality management system (QMS). Developed and published by the International Organization for Standardization (ISO), ISO 9001:2015 is the most current edition of the standard. This standard is applicable to organizations across various industries and sizes, providing a framework that aims to ensure consistent quality in products and services, aligning with customer expectations and regulatory compliance.
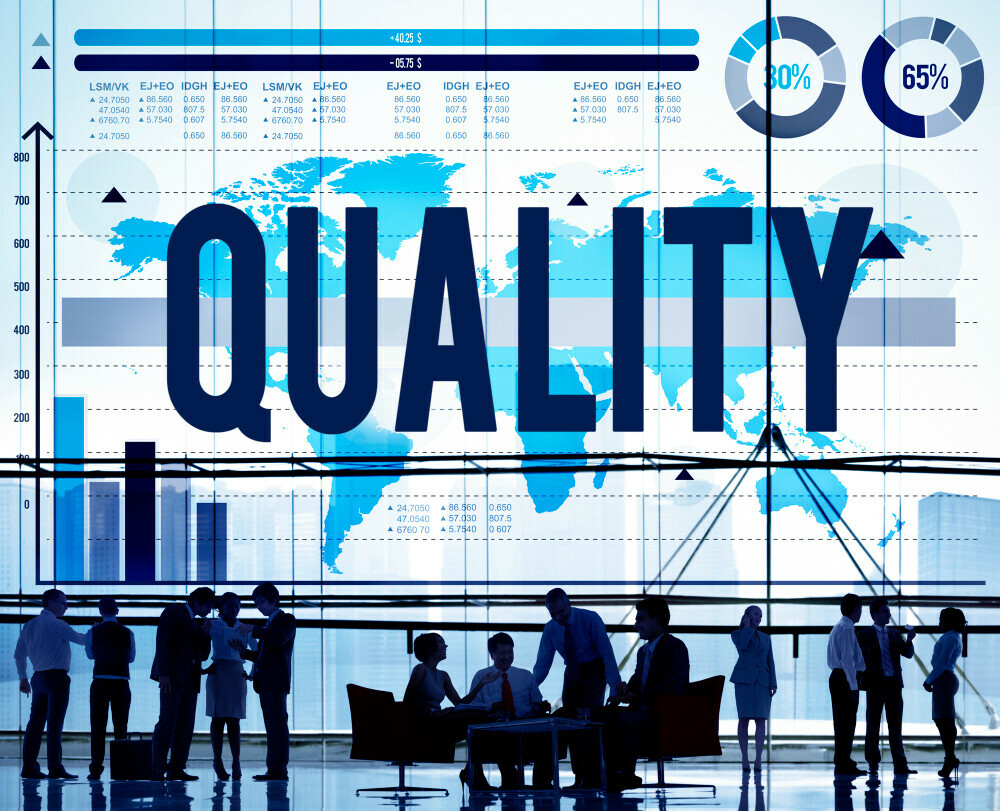
ISO 9001 is based on a number of quality management principles, including a strong customer focus, the involvement of high-level organization management, a process approach, and ongoing improvement. Implementing these principles into an organization’s operations is central to achieving ISO 9001 certification. In addition to outlining the QMS requirements, the ISO 9001:2015 standard also encourages organizations to enhance their performance continuously and provides a roadmap for maintaining and improving quality standards.
Key Takeaways
- ISO 9001:2015 is designed to help organizations ensure quality and enhance customer satisfaction.
- The standard emphasizes leadership engagement and a process-oriented approach for effective quality management.
- Continuous improvement is a fundamental goal of ISO 9001, fostering an environment of sustained quality enhancement.
What is ISO 9001?
The cornerstone of any thriving small enterprise is the confidence it instills in its customers and clients. The ISO 9001 Standard for Quality is instrumental in aiding organizations to establish, deploy, and uphold an effective Quality Management System (QMS) that steers everyday business operations.
Book a FREE 45-Minute Consultation
During the Consultation We Will Give You a Clear Direction and Path For You to Move Forward with Your Certification or Accreditation Goals
Watch the video below to get a great overview of ISO 9001 Explained in an easy-to-understand format.
A QMS aligned with ISO 9001 enables businesses to continuously refine their daily operations while setting precise, long-term objectives aimed at success. Driven by the rigorous quality demands of the standard, this QMS becomes a pivotal tool in steering a company towards its growth goals—enhancing customer experiences and elevating their satisfaction consistently.
Spanning across ten clauses, the ISO standard directs organizations towards bolstered internal processes and organizational culture enhancement. This text delves into the fundamental concept of ISO 9001, elucidating the essentials of the requirements and the pathway to obtaining certification.
Achieving ISO 9001 certification is a strategic endeavor that requires meticulous planning and an understanding of the certification process. This section will guide you through the essential steps and preparations needed to navigate the certification landscape.
Understanding the Certification Process: Steps and Timeline
The certification process for ISO 9001 involves a series of steps, typically starting with preparation and training. You’ll need to perform a gap analysis to determine where your quality management system (QMS) stands against ISO 9001 requirements. Following this, document development and implementation of procedures is essential, covering all clauses mandated by the standard. An internal audit is then conducted to ensure that your organization is ready for external scrutiny. Finally, an external audit is performed by a certification body, after which certification may be granted if your QMS meets all requirements. The timeline can vary, but it usually takes from three to six months, depending on your organization’s size and complexity.
Selecting a Credible ISO 9001 Registrar or Certification Body
When choosing a certification body, ensure they are accredited and have a good reputation in the industry. Check their experience in your sector and verify the skills and qualifications of their auditors. It’s crucial to select a body that aligns with your organizational values and one you feel comfortable working with throughout the certification process.
Preparation Tips for the Initial Certification Audit
Prepare meticulously for your initial certification audit by:
- Training all involved employees about ISO 9001 requirements and their role in compliance.
- Developing a comprehensive QMS documentation that correctly interprets and applies ISO 9001 standards.
- Ensuring all processes are fully implemented and operational.
- Conducting internal audits to identify and fix non-compliance issues.
- Creating a clear agenda for the certification audit, highlighting areas ready for evaluation.
Common Challenges Businesses Face During Certification and How to Overcome Them
Businesses often encounter certain challenges like:
- Understanding the complexity of ISO 9001 requirements. Overcome this by investing in ISO 9001 employee training for your team or hiring a consultant.
- Documentation can be taxing. Simplify this by using templates and tools that suit your organization’s needs and ensure accuracy.
- Resistance to change among staff. Address this through effective communication and demonstrating the value of ISO 9001 certification.
By being well-prepared and understanding common hurdles, your path to ISO 9001 certification should be straightforward and successful.
Fundamentals of ISO 9001: Clauses and Requirements
ISO 9001:2015 defines the criteria for a quality management system (QMS) and is constructed around seven key quality principles and a series of clauses tailored to enhance business processes. Your comprehension of these elements is crucial for implementing a robust QMS.
Detailed Review of ISO 9001 Structure and the Seven Quality Management Principles
ISO 9001 adopts a process approach, which integrates the seven quality management principles including customer focus, leadership, engagement of people, process approach, improvement, evidence-based decision-making, and relationship management. These principles are cornerstones that inform the structure of the ISO standard and guide the development and implementation of an effective QMS.
Navigating the Key Clauses of ISO 9001, from Context of the Organization to Improvement
When you navigate through ISO 9001, there are ten clauses to focus on:
- Scope
- Normative References
- Terms and Conditions
- Context of the Organization: This sets the stage for the QMS, requiring you to define external and internal issues, interested parties, and the scope of the system.
- Leadership: Top management’s commitment is emphasized here, with a requirement to establish a quality policy and objectives aligned with the business strategy.
- Planning: This involves addressing risks and opportunities and setting quality objectives.
- Support: You’ll need to look at resources needed, including human resources and infrastructure, for maintaining and improving your QMS.
- Operation: Outlines how to plan, implement, and control the processes needed to meet service and product requirements.
- Performance Evaluation: Monitoring the QMS’s effectiveness is critical—this includes internal audits and management reviews.
- Improvement: The standard closes with a requirement for continuous improvement, a tenet of the ISO 9001 framework.
Italicize the “seven quality management principles,” “risks and opportunities,” and “continuous improvement” to emphasize these key concepts.
The Role of Leadership and Management Commitment in ISO 9001
The leadership clause (5) underlines that your top management must demonstrate leadership and commitment with respect to the QMS. It stresses a management-led approach to quality where leaders not only set policies and objectives but also walk the talk by integrating ISO 9001 requirements into business processes and guiding the direction of the organization’s quality management.
Bold the phrase “management-led” to convey the importance of active management involvement.
Exploring Requirements for Planning, Support, and Operation Within the Standard
When planning your QMS, ISO 9001 mandates you to align it with strategic business practices, focusing on quality objectives and risk-based thinking. Ensure that your QMS is provided with the necessary support in terms of people, technology, and processes. During operations, be diligent with planning and control, adapting a framework that offers consistent and reliable products and services to your customers.
Use bullet points to highlight the requirements for support:
- Provide proper resources and infrastructure
- Ensure personnel competence
- Awareness and communication
- Documented information – creation, updating, and control
As you implement ISO 9001:2015 into your business, keep these structured clauses in mind, and remember that the shift from ISO 9001:2008 to ISO 9001:2015 incorporated these principles more explicitly, to emphasize the importance of the process approach and continuous improvement.
Implementation Strategies for a Robust ISO 9001 System
To successfully implement an ISO 9001 Quality Management System (QMS), a strategic approach must balance firm adherence to standards with adaptive practices tailored to your organization’s unique context. This involves a methodical planning phase, high levels of staff engagement, and the establishment of monitoring and continuous improvement mechanisms.
Best Practices for Implementing an ISO 9001 Compliant Quality Management System
Understand the requirements: Before implementation, thoroughly grasp the ISO 9001 requirements to align them with your business processes.
- Gap Analysis: Conduct a gap analysis to determine the discrepancies between current processes and ISO 9001 standards.
- Align Organizational Goals: Ensure your quality policy and objectives reflect the organization’s overall mission and context.
- Resource Allocation: Dedicate appropriate resources including personnel, technology, and financial assets for effective implementation.
Building a Culture of Quality: Employee Engagement and Training
Engagement: Involve employees at all levels to engender ownership of the QMS.
- Training: Provide comprehensive training to upskill your workforce, emphasizing the importance of quality and their role in achieving it.
- Communication: Regularly communicate the benefits and goals of the ISO 9001 QMS to keep quality at the forefront of everyone’s agenda.
Leveraging Documentation and Records for ISO 9001 Success
Document Control: Develop and enforce a document management system to maintain control over all QMS documents.
- Records Management: Keep accurate records as evidence of conformity to requirements, and to demonstrate the effective operation of the QMS.
- Auditable Data: Ensure all data and information is readily available for audits to verify system effectiveness.
Measuring, Monitoring, and Reporting Performance Against ISO 9001 Standards
KPIs and Measurement: Establish Key Performance Indicators (KPIs) that are directly tied to quality objectives, and the overall effectiveness of the QMS.
- Regular Audits: Conduct internal audits to measure compliance and effectiveness of the QMS, and to encourage continuous improvement.
- Data Analysis: Utilize data from monitoring activities for evidence-based decision making, focusing on areas where you can enhance quality and performance.
By following these strategies, you can build a QMS that not only complies with ISO 9001 but also becomes a cornerstone of your organization’s continual growth and improvement.
Continuous Improvement and ISO 9001: Beyond Compliance

As you explore the ISO 9001 standard, understanding that continuous improvement is not just a requirement but a strategic approach to outperform and achieve business excellence is essential. This perspective allows your organization to transition from mere compliance to becoming a performance leader in your industry.
The Philosophy and Techniques of Continuous Improvement Within ISO 9001
ISO 9001 embeds the philosophy of continuous improvement within its Quality Management System (QMS). The Plan-Do-Check-Act (PDCA) cycle is a fundamental technique for driving improvement. You plan by setting objectives and processes, do by implementing the plan, check by monitoring and measuring results against objectives, and then act to improve and refine your processes. This cycle ensures that continuous improvement is systematic and ingrained in organizational operations.
Real-World Examples of Businesses Benefiting from ISO 9001 Continuous Improvement
Businesses across various sectors have reaped substantial benefits by incorporating the continuous improvement model of ISO 9001. For instance, a manufacturing firm may report a 15% increase in productivity after streamlining their production lines. Another example could be a service provider increasing customer satisfaction by 20% due to enhanced service delivery processes. These real-world cases demonstrate how commitment to continuous improvement can lead to significant gains in efficiency and customer confidence.
Incorporating Customer Feedback and Data Analysis into Your Improvement Strategies
Your QMS should prioritize customer focus by integrating customer feedback and data analysis into improvement strategies. By frequently gathering and evaluating feedback, you address customer requirements and expectations head-on. Coupled with data analysis, which provides empirical insights into process performance, you can identify areas ripe for improvement, leading to increased efficiency and customer satisfaction.
Striving for Excellence: Moving from Compliance to Performance Leadership
While regulatory and customer requirements may set the baseline, striving for excellence means looking beyond them. Embrace the seven Quality Management Principles (QMPs), including a strong customer focus and a factual approach to decision-making. Use these principles to elevate your processes and embed a culture of quality that resonates confidence to your customers, thus fostering a reputation for performance leadership beyond mere compliance.
Frequently Asked Questions

This section addresses some of the most common inquiries about ISO 9001, providing you with concise and clear information to understand this quality management standard.
What are the core elements of the ISO 9001 Quality Management System?
The ISO 9001 Quality Management System (QMS) is grounded in a set of core elements including a strong customer focus, leadership commitment, engagement of people, process approach, improvement, evidence-based decision-making, and relationship management.
How can a company become ISO 9001 certified?
To become ISO 9001 certified, your company must implement a QMS that complies with the requirements of the standard, then successfully pass an audit by an accredited certification body.
What are the seven principles that underlie the ISO 9001:2015 edition?
The seven principles that form the basis of ISO 9001:2015 are customer focus, leadership, engagement of people, process approach, improvement, evidence-based decision-making, and relationship management.
In what ways does the ISO 9001:2015 edition differ from previous versions?
The ISO 9001:2015 edition differs from its predecessors by emphasizing risk-based thinking, integrating the QMS into the organization’s strategic direction, and offering a more flexible approach to documentation.
How do ISO 9001 standards benefit businesses and their customers?
ISO 9001 standards benefit businesses by enhancing efficiency and customer satisfaction through standardized processes and continual improvement, while customers enjoy consistent and higher quality products and services.
What are the required documentation and records for ISO 9001 compliance?
For ISO 9001 compliance, your company is required to maintain documented information needed to support the operation of processes and retain evidence that the processes are being carried out as planned. Documentation may include a quality policy, objectives, quality manual, and records of training, corrective actions, and audit results.
Understanding The ISO 9001 Standard- Conclusion
The ISO 9001 standard is a pivotal tool for businesses seeking to enhance their quality management systems. It offers a framework that not only streamlines processes but also boosts efficiency and customer satisfaction. By adhering to its principles, organizations can foster a culture of continuous improvement, ensuring long-term success in a competitive marketplace. Implementing ISO 9001 demonstrates a commitment to quality, which can lead to increased trust and credibility among clients and stakeholders. Overall, this standard is a key ingredient for achieving business excellence and sustainable growth.
In addition to fostering operational excellence, ISO 9001 helps organizations to navigate the complexities of modern business landscapes. By establishing a robust quality management system, companies are better equipped to identify risks and opportunities, ensuring adaptability in a rapidly changing world. This standard not only improves internal processes but also enhances customer relations by consistently meeting, if not exceeding, their expectations. In essence, ISO 9001 is not just a certification; it’s a strategic tool that propels businesses towards sustainable development and market leadership. Embracing this standard is a definitive step towards creating a resilient and prosperous future for any organization.